ACC Coatings wants our customers to be able to identify and fix some of the most common coating issues that occur on the line. When something goes awry, use this page as a checklist to make sure you are doing things right before making assumptions about your equipment or coating applications.
Troubleshooting
Identify and Fix Common Coating Issues

A Brief Guide to Coating Troubleshooting from ACC
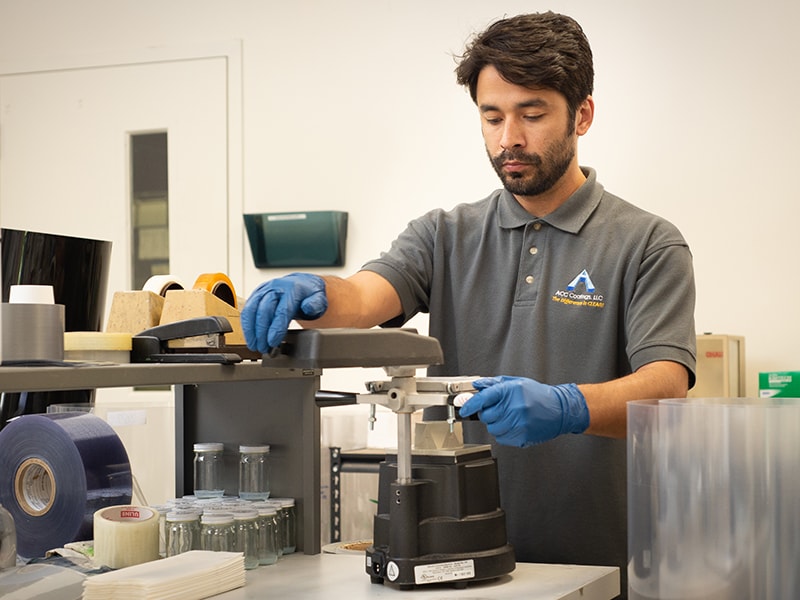
Recommended Procedures for Common Coating Issues
Most of the troubleshooting our customers do involves one or more of the following issues. Many of the operational remedies identified should be common practice but they tend to get overlooked in the minutiae of daily operations.
The information below should help you identify the problems you’re having and provide suggestions for alleviating them. Please feel free to reach out to us if you know what the problem is but you are unable to remedy it. We’re happy to help!
Regarding Storage
- Avoid storing drums and totes of coatings where they are exposed to extreme temperatures.
- Ensure that the containers are sealed when not in use to avoid contamination and evaporation.
Mixing Solution Prior to Use
- Some phase separation and soft settling may occur when the material is stored for more than a few days. A slow stir using a pneumatic mixer quickly alleviates this problem.
- Prior to use, mix drums that contain coating for 15 – 30 minutes with gentle agitation. If dilution is necessary, mix the dilution using gentle agitation, too.
- Note that exceptions exist. Please follow the instructions shown on the product’s Technical Data Sheets (TDS) or contact your ACC Coatings technical representative.
Excessive Foaming
- Confirm what type of fluid management system pump is being used to feed the coater or coating station. Because the high sheer and air introduced in centrifugal-style pumps can cause foaming, ACC Coatings recommends the use of diaphragm or peristaltic pumps for fluid management.
- Ensure that the coating is gently placed or poured into tanks and pans. Aggressive pours or a waterfall effect (i.e., caused by increasing the distance from feed outlets to the sump or coating surface) can also produce a high-sheer effect from gravity, introducing air and generating foam.
Excessive Haze on Clear Coatings
Insufficient drying can cause haze. Be sure that sufficient heat and/or ventilation is available so the coating dries before the coated sheets contact the turn/idler rolls and other downstream equipment. The coating should be tack-free prior to being wound into roll stock.
A quick solution is to aim a floor fan in the direction of the freshly coated sheet; this helps immensely in reducing haze and buildup on equipment over time. Pairing short-wave IR heaters with blowers is the most effective means for ensuring adequate drying while maintaining high throughput on production lines.
- Overapplication of the coating can result in excessive haze. When using a roll coater, tighten the pressure between the doctor roll and the applicator roll to apply less coating. If using a dip/squeegee coater, tighten the pressure between the nip rollers to prevent overapplication.
Ensure that the solids levels of the coating have not risen. Keep the sumps/pans covered to help reduce evaporation over time. Monitor solids levels using refractometers. ACC Coatings assists customers in developing a quality control process, and we help generate calibration curves for our products.